原油常减压蒸馏装置的工艺特征
原油蒸馏是
否采用初馏塔应根据具体条件对有关因素进行综合分析后
决定。
下面讨论初馏塔的作用。
含轻馏分较多的原油在经过换热器被加热时,随着温度的升高,轻馏分汽化,从而增大了原油通过换热器和管路的阻力,这就要求提高原油输送泵的扬程和换热器的压力等级,也就是增加了电能消耗和设备投资。
如果将原油经换热过程中已汽化的轻组分及时分离出来, 让这部分馏分不必再进入常压炉去加热。这样一是能减少原油管路阻力, 降低原油泵出口压力;二是能减少常压炉热负荷,二者均有利于降低装置能耗。因此,当原油含汽油馏分接近或大于 20%时,可采用初馏塔。
当原油因脱水效果波动而引起含水量高时,水能从初馏塔塔顶分出,使得常压塔操作免受水的影响,保证产品质量合格。
对含砷量高的原油如大庆原油(As>2000µg/g),为了生产重整原料油,必须设置初馏塔。重整催化剂极易被砷中毒而永久失活,重整原料油的砷含量要求小于200µg/g。如果进入重整装置的原料的含砷量超过 200µg/g,则仅依靠预加氢精制是不能使原料达到要求的。
此时,原料应在装置外进行预脱砷,使其含砷量小于 200µg/g 以下后才能送入重整装置。
重整原料的含砷量不仅与原油的含砷量有关,而且与原油被加热的温度有关。例如在加工大庆原油时,初馏塔进料温度约 230℃,只经过一系列换热,温度低且受热均匀,不会造成砷化合物的热分解,由初馏塔顶得到的重整原料的含砷量小于 200µg/g。若原油加热到 370℃直接进入常压塔,则从常压塔顶得到的重整原料的含砷量通常高达 1500µg/g。重整原料含砷量过高不仅会缩短预加氢精制催化剂的使用寿命, 而且有可能保证不了精制后的含砷量降至 1µg/g 以下。因此,国内加工大庆原油的炼油厂一般都采用初馏塔,并且只取初馏塔
当加工含硫原油时,在温度超过 160~180℃的条件下,某些含硫化合物会分解而释放出 H2S,原油中的盐分则可能水解而析出 HCl,造成蒸馏塔顶部、汽相馏出管线与冷凝冷却系统等低温部位的严重腐蚀。设置初馏塔可使大部分腐蚀转移到初馏塔系统,从而减轻了常压塔顶系统的腐蚀,这在经济上是合理的。但是这并不是从根本上解决问题的办法。实践证明,加强脱盐、脱水和防腐蚀措施,可以大大减轻常压塔的腐蚀而不必设初馏塔。
原油的常压蒸馏就是原油在常压(或稍高于常压)下进行的蒸馏,所用的蒸馏设备叫做原油常压精馏塔,它具有以下工艺特点:
原油通过常压蒸馏要切割成汽油、煤油、轻柴油、重柴油和重油等四、 五种产品馏分。按照一般的多元精馏办法, 需要有N-1个精馏塔才能把原料分割成N个馏分。但是在石油精馏中, 各种产品本身依然是一种复杂混合物, 它们之间的分离精确度并不要求很高, 两种产品之间需要的塔板数并不多, 因而原油常压精馏塔是在塔的侧部开若干侧线以得到如上所述的多个产品馏分, 就像N个塔叠在一起一样, 它的精馏段相当于原来N个简单塔的精馏段组合而成,而其下段则相当于最下一个塔的提馏段,故称为复合塔(见图2—21)。

原油经过常压蒸馏可得到沸点范围不同的馏分,如汽油、煤油、柴油等轻质馏分油和常压重油,这些产品仍然是复杂的混合物(其质量是靠一些质量标准来控制的,如汽油馏程的干点不能高于 205℃) 。35℃~150℃是石脑油或重整原料,130℃~250℃是煤油馏分,250℃~300℃是柴油馏分,300℃~350℃是重柴油馏分,可作催化裂化原料。>350℃是常压重油。
对石油精馏塔,提馏段的底部常常不设再沸器,因为塔底温度较高,一般在 350℃左右,在这样的高温下,很难找到合适的再沸器热源。因此,通常向底部吹入少量过热水蒸汽,以降低塔内的油汽分压,使混入塔底重油中的轻组分汽化,这种方法称为汽提。汽提所用的水蒸汽通常是 400℃~450℃,约为 3MPa的过热水蒸汽。
在复合塔内,汽油、煤油、柴油等产品之间只有精馏段而没有提馏段,这样侧线产品中会含有相当数量的轻馏分,这样不仅影响侧线产品的质量,而且降低了轻馏分的收率。所以通常在常压塔的旁边设置若干个侧线汽提塔,这些汽提塔可重叠起来, 但相互之间是隔开的,侧线产品从常压塔中部抽出,送入汽提塔上部,从该塔下注入水蒸汽进行汽提,汽提出的低沸点组分同水蒸汽一道从汽提塔顶部引出返回主塔,侧线产品由汽提塔底部抽出送出装置。
在有些情况下,侧线的汽提塔不采用水蒸气而仍像正规的提馏段那样采用再沸器。这种做法是基于以下几点考虑:
(1)侧线油品汽提时,产品中会溶解微量水分,对有些要求低凝点或低冰点的产品如航空煤油可能使冰点升高,采用再沸提馏可避免此弊病。
(2)汽提用水蒸气的质量分数虽小(通常为侧线产品的 2%~3%),但水的相对分子质量比煤油、柴油低数十倍,因而体积流量相当大,增大了塔内的气相负荷。采用再沸提馏代替水蒸气汽提有利于提高常压塔的处理能力。
(3)水蒸气的冷凝潜热很大,采用再沸提馏有利于降低塔顶冷凝器的负荷。
采用再沸提馏代替水蒸气汽提会使流程设备复杂些,因此采用何种方式要具体分析。至于侧线油品用作裂化原料时则可不必汽提。
常压塔进料汽化段中未汽化的油料流向塔底,这部分油料中还含有相当多的<350℃轻馏分。因此,在进料段以下也要有汽提段,在塔底吹入过热水蒸气以使其中的轻馏分汽化后返回精馏段, 以达到提高常压塔拔出率和减轻减压塔负荷的目的。塔底吹入的过热水蒸气的质量分数一般为 2%~4%。常压塔底不可能用再沸器代替水蒸气汽提,因为常压塔底温度一般在 350℃左右,如果用再沸器,很难找到合适的热源,而且再沸器也十分庞大。减压塔的情况也是如此。
由于常压塔塔底不用再沸器,热量来源几乎完全取决于加热炉加热的进料。汽提水蒸气(一般约 450℃)虽也带入一些热量,但由于只放出部分显热,且水蒸气量不大,因而这分热量是不大的。全塔热平衡的情况引出以下几个问题:
(1)常压塔进料的汽化率至少应等于塔顶产品和各侧线产品的产率之和,否则不能保证要求的拔出率或轻质油收率。至于普通的二元或多元精馏塔,理论上讲进料的汽化率可以在 0~1 之间任意变化而仍能保证产品产率。在实际设计和操作中,为了使常压塔精馏段最低一个侧线以下的几层塔板(在进料段之上)上有足够的液相回流以保证最低侧线产品的质量,原料油进塔后的汽化率应比塔上部各种产品的总收率略高一些。高出的部分称为过汽化度。常压塔的过汽化度一般为 2%~4%。实际生产中,只要侧线产品质量能保证,过汽化度低一些是有利的, 这不仅可减轻加热炉负荷, 而且由于炉出口温度降低可减少油料的裂化。
(2)在常压塔只靠进料供热,而进料的状态(温度、汽化率)又已被规定。因此,常压塔的回流比是由全塔热平衡决定的,变化的余地不大。常压塔产品要求的分离精确度不太高,只要塔板数选择适当,在一般情况下,由全塔热平衡所确定的回流比已完全能满足精馏的要求。普通的二元系或多元系精馏与原油精馏不同,它的回流比是由分离精确度要求确定的,至于全塔热平衡,可以通过调节再沸器负荷来达到。在常压塔的操作中,如果回流比过大,必然会引起塔的各点温度下降、馏出产品变轻、拔出率下降。
(3)在原油精馏塔中,除了采用塔顶回流时,通常还设置 1~2 个中段循环回流,即从精馏塔上部的精馏段引出部分液相热油, 经与其它冷流换热或冷却后再返回塔中,返回口比抽出口通常高 2~3层塔板。
中段循环回流的作用是,在保证产品分离效果的前提下,取走精馏塔中多余的热量,这些热量因温位较高,因而是价值很高的可利用热源。采用中段循环回流的好处是,在相同的处理量下可缩小塔径,或者在相同的塔径下可提高塔的处理能力。
在普通的二元和多元精馏塔的设计计算中,为了简化计算,对性质及沸点相近的组分所组成的体系作出了恒分子回流的近似假设, 即在塔内的气、 液相的摩尔流量不随塔高而变化。
这个近似假设对原油常压精馏塔是完全不能适用的。石油是复杂混合物,各组分间的性质可以有很大的差别,它们的摩尔汽化潜热可以相差很远,沸点之间的差别甚至可达几百度。如常压塔顶和塔底之间的温差就可达 250℃左右。显然,以精馏塔上、下部温差不大,塔内各组分的摩尔汽化潜热相近为基础所作出的恒分子回流这一假设对常压塔是完全不适用的。
原油在常压蒸馏的条件下,只能够得到各种轻质馏分。常压塔底产物即常压重油,是原油中比较重的部分,沸点一般高于 350℃,而各种高沸点馏分,如裂化原料和润滑油馏分等都存在其中。要想从重油中分出这些馏分,就需要把温度提到 350℃以上,而在这一高温下,原油中的稳定组分和一部分烃类就会发生分解,降低了产品质量和收率。为此,将常压重油在减压条件下蒸馏,蒸馏温度一般限制在 420℃以下。降低压力使油品的沸点相应下降,上述高沸点馏分就会在较低的温度下汽化, 从而避免了高沸点馏分的分解。减压塔是在压力低于 100kPa 的负压下进行蒸馏操作。
根据生产任务的不同,减压塔可分为润滑油型和燃料型两种,见图 2—22和图 2—23。
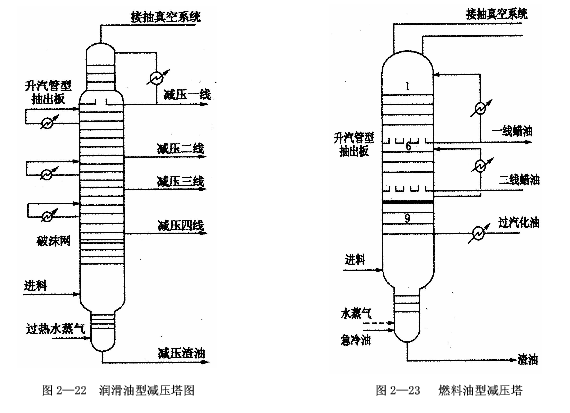
润滑油型减压塔是为了提供黏度合适、残炭值低、色度好和馏程较窄的润滑油料。燃料型减压塔主要是为了提供残炭值低和金属含量低的催化裂化和加氢裂化原料,对馏分组成的要求是不严格的。无论哪种类型的减压塔,都要求有尽可能高的拔出率。为了提高汽化段的真空度,除了需要有一套良好的塔顶抽真空系统外,一般还采取以下几种措施。
(1)降低从汽化段到塔顶的流动压降。这主要依靠减少塔板数和降低气相通过每层塔板的压降来实现。
(2)降低塔顶油气馏出管线的流动压降。为此,减压塔塔顶不出产品,塔顶管线只供抽真空设备抽出不凝气用。因为减压塔顶没有产品馏出,故只采用塔顶循环回流而不采用塔顶冷回流。
(3)减压塔塔底汽提蒸汽用量比常压塔大,其主要目的是降低汽化段中的油气分压。近年来,少用或不用汽提蒸汽的干式减压蒸馏技术有较大的发展。
(4)降低转油线压降,通过降低转油线中的油气流速来实现。减压塔汽化段温度并不是常压重油在减压蒸馏系统中所经受的最高温度, 此最高温度的部位是在减压炉出口。为了避免油品分解,对减压炉出口温度要加以限制,在生产润滑油时不得超过395℃,在生产裂化原料时不超过 400~420℃,同时在高温炉管内采用较高的油气流速以减少停留时间。
(5)缩短渣油在减压塔内的停留时间。塔底减压渣油是最重的物料,如果在高温下停留时间过长,则其分解、缩合等反应进行得比较显著。其结果,一方面生成较多的不凝气使减压塔的真空度下降;另一方面会造成塔内结焦。因此,减压塔底部的直径通常缩小,以缩短渣油在塔内的停留时间。此外,有的减压塔还在塔底打入急冷油以降低塔底温度,减少渣油分解、结焦的倾向。
由于上述各项工艺特征,从外形来看,减压塔比常压塔显得粗而短。此外,减压塔的底座较高,塔底液面与塔底油抽出泵入口之间的位差在10m 左右,这主要是为了给热油泵提供足够的灌注头。
减压塔之所以能在减压下操作, 是因为在塔顶设置了一个抽空真空系统, 将塔内不凝气、注入的水蒸气和极少量的油气连续不断地抽走,从而形成塔内真空。减压塔的抽真空设备可以用蒸汽喷射器(也称蒸汽喷射泵或抽空器)或机械真空泵。在炼油厂中的减压塔广泛地采用蒸汽喷射器来产生真空,图 2—24 是常减压蒸馏装置常用的蒸汽喷射器抽真空系统的流程。
减压塔顶出来的不凝气、水蒸气和少量油气首先进入一个管壳式冷凝器。水蒸气和油气被冷凝后排入水封池,不凝气则由一级喷射器抽出,从而在冷凝器中形成真空。由一级喷射器抽来的不凝气再排入一个中间冷凝器,将一级喷射器排出的水蒸气冷凝。不凝气再由二级喷射器抽走而排入大气。为了消除因排放二级喷射器的蒸汽所产生的噪音及避免排出的蒸汽的凝结水洒落在装置平台上,通常再设一个后冷器将水蒸气冷凝而排入水阱,而不凝气则排入大气。
冷凝器是在真空下操作的。为了使冷凝水顺利地排出,排出管内水柱的高度应足以克服大气压力与冷凝器内残压之间的压差以及管内的流动阻力。通常此排液管的高度至少应在10m 以上,在炼油厂俗称此排液管为大气腿。
图 2—24 中的冷凝器是采用间接冷凝的管壳式冷凝器, 故通常称为间接冷凝式二级抽真空系统。它的作用在于使可凝的水蒸气和油气冷凝而排出,从而减轻喷射器的负荷。冷凝器本身并不形成真空,因为系统中还有不凝气存在。
另外,最后一级冷凝器排放的不凝气中,气体烃(裂解气)占 80%以上,并含有硫化物气体,造成大气污染和可燃气的损失。国内外炼油厂都开始回收这部分气体,把它用作加热炉燃料,即节约燃料,又减少了对环境的污染。
蒸汽喷射器由喷嘴、扩张器和混合室构成。高压工作蒸汽进入喷射器中,先经收缩喷嘴将压力能变成动能,在喷嘴出口处可以达到极高的速度(1000~1400m/s), 使混合室形成了高度真空。不凝气从进口处被抽吸进来,在混合室内与驱动蒸汽混合并一起进入扩张器,扩张器中混合流体的动能又转变为压力能,使压力略高于大气压,混合气才能从出口排出。
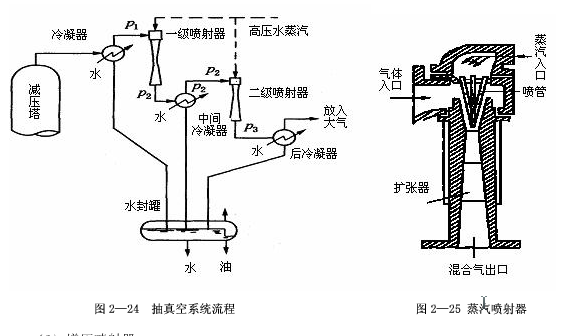
在抽真空系统中,不论是采用直接混合冷凝器、间接式冷凝器还是空冷器,其中都会有水存在。水在其本身温度下有一定的饱和蒸气压,故冷凝器内总是会有若干水蒸气。因此,理论上冷凝器中所能达到的残压最低只能达到该处温度下水的饱和蒸气压。
减压塔顶所能达到的残压应在上述的理论极限值上加上不凝气的分压、 塔顶馏出管线的压降、冷凝器的压降。所以减压塔顶残压要比冷凝器中水的饱和蒸气压高,当水温为 20℃时, 冷凝器所能达到的最低残压为 0.0023 MPa, 此时减压塔顶的残压就可能高于 0.004MPa。
实际上,20℃的水温是不容易达到的,二级或三级蒸气喷射抽真空系统,很难使减压塔顶达到 0.004MPa 以下的残压。如果要求更高的真空度,就必须打破水的饱和蒸气压这个极限。因此,在塔顶馏出气体进入一级冷凝之前,再安装一个蒸气喷射器使馏出气体升压,如图 2—26 所示。
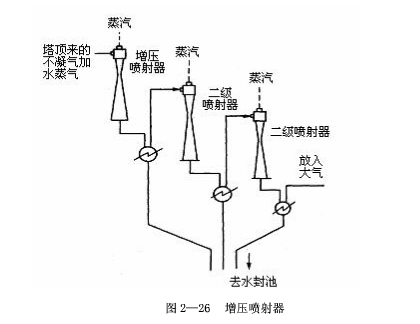
由于增压喷射器前面没有冷凝器,所以塔顶真空度就能摆脱水温限制, 而相当于增压喷射器所能造成的残压加上馏出线压力降,使塔内真空度达到较高程度。但是,由于增压喷射器消耗的水蒸气往往是一级蒸汽喷射器消耗蒸气量的四倍左右,故一般只用在夏季、 水温高、冷却效果差,真空度很难达到要求的情况下或干式蒸馏情况下。
文章来源:催化人