Moldex3D模流分析之运用模流分析软件 增进精密光学新制程验证效率

大纲
精密光学组件的射出成型技术发展至今已相当成熟,然而随着成品精度的要求越来越高,包括残留应力分布、翘曲及凹痕等问题都必须严格控制,因此成型技术的改良势在必行。台科大精密制造实验室期望开发模内微压缩成型(In-Mold Micro Compression, IMMC)制程,以改善射出成型所产生的缺陷。在开发之前,先藉由Moldex3D的射出压缩成型模块进行分析,判断产品是否确实达到优化,以评估开发新制程的可行性。分析结果发现模内微压缩成型在产品凹痕、体积收缩和集光效果等方面都有显著改善;经实际试模和量测之后,同时也验证Moldex3D分析的高准确度。
挑战
压力分布不均
体积收缩率过高
翘曲变形问题
解决方案
藉由Moldex3D射出压缩成型模块进行传统射出制程和IMMC制程的分析和比较,以决定是否应用新的制程。
效益
压力分布均匀度大幅改善
产品光照度提升7.35%
体积收缩率由6.62%降低至4.25%
案例研究
图一 本案例的复合式棱镜为塑料制的集光组件
复合式棱镜是自然导光系统中的集光组件,用于室外或建筑物屋顶收集阳光(图一)。为了提升产品的导光效率,浇口位置必须避开导光处,设计于产品薄端,却因此不利压力传递和塑料流动。此外,为了提升导光效果,产品中有两处狭缝设计(图二),造成局部模温较低。塑料流经模温较低处时容易凝固而难以流动,导致压力传递不易,体积收缩率也较高,使成品后端产生明显凹痕,影响集光、传光与出光的效果。为解决这些难题,台科大精密制造实验室运用Moldex3D模流分析软件,评估开发模内阶段式射压成型制程,是否能够获得较优化的产品。
图二 产品有两处狭缝设计,会导致流动不平衡情形
首先藉由Moldex3D来进行射出成型制程的分析。在凹痕指标的分析中,图三(左图)显示产品厚段处的凹痕指标大,原因是内部塑料温度高,使得表面向内收缩而导致凹痕。图三(右图)则显示产品第三齿处有较大的凹痕位移,表示产品末端体积收缩率大,以致平面度不佳,降低集光效果。
图三 进行射出成型制程分析,保压结果中的凹痕指标(左)及凹痕位移(右)情形
接下来利用Moldex3D进行模内阶段式射压成型的分析。分析结果发现,IMMC制程的体积收缩率,比传统制程少了 18.9%(图四)。在翘曲变形的部分,从翘曲分析结果中的Z方向位移,也可看出IMMC制程比射出成型优化了71%(图五)。
(a)
(b)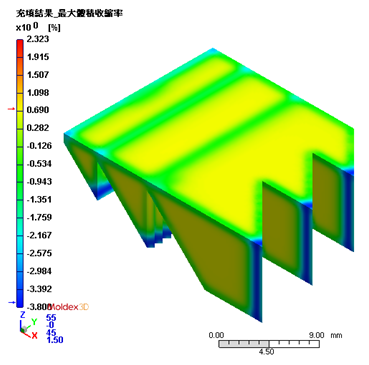
图四 保压结果的体积收缩率比较:图(a)为传统射出制程,体积收缩率在-2.9%~2.323%之间;
图(b)为IMMC制程,体积收缩率在-3.7%~0.69%之间。
(a)
(b)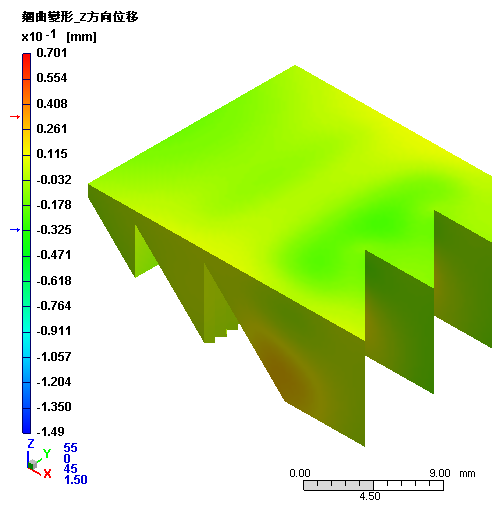
图五 翘曲分析中的Z方向位移:图(a)为传统射出制程,Z方向位移范围为-1.497~0.701mm;
图(b)为IMMC制程,Z方向位移范围为-0.325~0.311mm。
比较两种制程的总和光弹条纹分析结果(图六)则可发现,传统制程在浇口处的光弹条纹变化剧烈,表示有较大的残留应力,应是使用较大的保压压力所造成。而在IMMC制程中,因为有模内压缩的辅助,可降低浇口压力,所以浇口处的条纹变化较不剧烈。

完成模流分析后,便进行实际试模,以验证Moldex3D分析结果的准确度。Moldex3D的分析与实际验证结果都显示,在射出成型制程中,产品的两狭缝会造成压力传递困难,造成产品后端有凹痕产生(图七)。改用模内阶段式射压成型(IMMC)制程后,可成功开发无凹痕的产品(图八)。
图七 Moldex3D凹痕模拟分析结果分析(图左)与实际试模(图右)结果高度一致
图八 模内阶段式射压成型开发的产品无表面缺陷
结论
在产品的光照度部分,实验室以LED灯泡照射方式进行验证。经六次取样,传统制程与射压制程的平均光照度分别为299Lux和321Lux,射压制程的光照度获得7.35%提升。最后使用光弹条纹量测机台进行光弹条纹的验证。从图九可发现,模流分析和实际实验结果高度吻合,也证明Moldex3D对光弹条纹预测分析准确度十分准确。
由以上量测结果可证明,Moldex3D的分析与实际试模结果有高度一致性,有助于验证新制程是否有助于开发复合式棱镜。若缺少Moldex3D模拟辅助成型这个过程,会浪费不必要的设计与加工费用;万一压缩制程无法如预期提升导光效果,开发过程的损失将难以估计。